发酵搅拌技术
搅拌器的主要作用
混合:将混溶的液体混合均匀,在整个发酵罐内形成均一的浓度分布。
传热:将发酵过程中产生的大量的热量移出发酵罐 (冷却盘管或者罐外螺旋板冷却夹套等)
气体分散:无菌空气通过气体喷射环或分布管引入发酵罐内。搅拌桨必须能够有效地将气体分散到液体中去,以促进微生物生长,生成最终产品。
桨型设计 :
必须兼顾剪切(有助于气体分散到液体中去)和宏观混合流动两方面。
桨型设计还应充分考虑产品的特性,根据产品对剪切的敏感性的不同,可分别选择高剪切搅拌桨或者低剪切搅拌桨。
高剪切型涡轮桨 – 适用于对剪切不敏感的产品
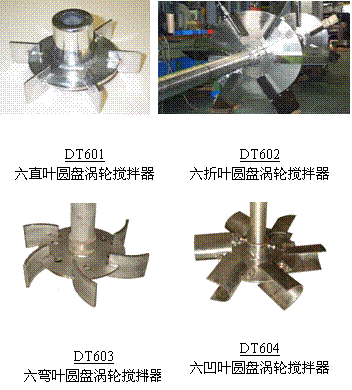
低剪切型涡轮桨– 适用于对剪切敏感的产品
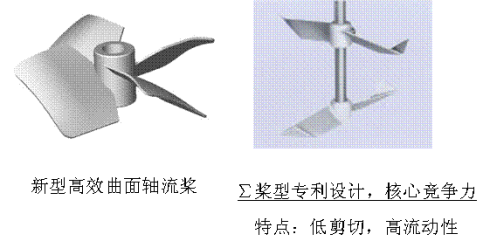
生物制药 -几种特殊的无菌级发酵搅拌桨
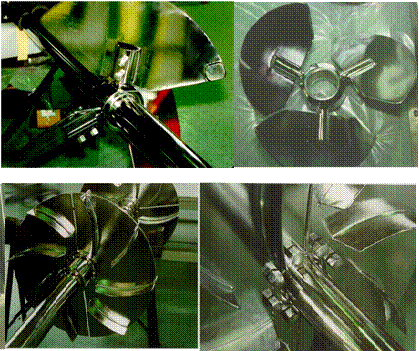
发酵罐内搅拌桨配置
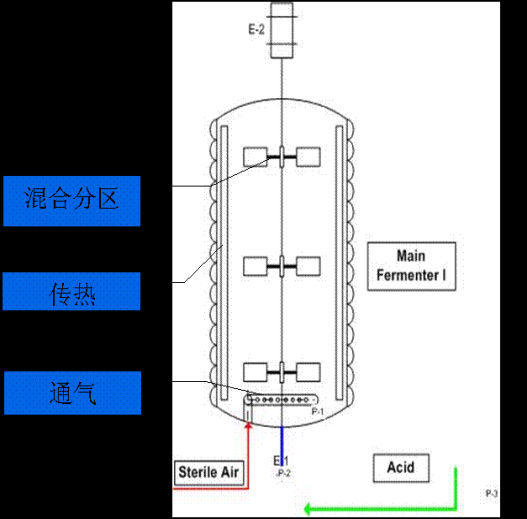
某公司 120m3 土霉素发酵罐现状
设备的直径为3800mm,直边高度为9300mm,上下为标准椭圆封头,全容积约120m3,装料体积约100m3。设备内设置六组换热管,垂直布置。
发酵罐的搅拌器采用四层六箭叶圆盘涡轮,桨叶直径1250mm,配备的电机功率为280kW,10级电机,采用皮带减速,搅拌转速分别为125rpm。
120m3 土霉素发酵罐存在的主要问题
1、能耗分配问题
由于发酵罐的气体进口位于发酵罐的底部,底部搅拌器(即第1个搅拌器)的气体剪切分散能力显得十分重要,搅拌的能量耗散应主要集中在此搅拌器,其他位置搅拌器的主要功能是维持气泡的分散状态和釜内的宏观混合及传热,能耗相对较小。而本发酵罐上下均为相同直径相同形状的搅拌器,消耗了同等的搅拌功率,显然本发酵罐各搅拌器的能耗分配是不合理的,上面几层搅拌器的剪切作用近乎于浪费。
2、桨型选择问题
原发酵罐的搅拌器采用四层箭叶圆盘涡轮,为常规的气体分散搅拌器。该搅拌器为径流桨,比较适合低粘体系小气量的搅拌,当气体流量增大时,其叶片背面形成气穴,表观密度下降,搅拌器由于“打滑”而功率下降,气体的分散能力削弱。右图为实验室结果,当气量到达1VVM时(单位体积液体中每分钟通过的气体量),图中6DT搅拌器(即六直叶圆盘涡轮)的功率下降近25%,同样六弯叶、六箭叶等圆盘涡轮的特性也基本相似。本发酵罐的通气量约为0.96VVM,搅拌器的气体处理能力已明显下降。所以本桨型不合理。
3、流型问题
当发酵液粘度较低时,其搅拌器的设计关键是气体的分散,良好气体的分散,可增加气含率、减小气泡直径、提高容积传质系数,从而提高空气中氧气的利用率,减小气体的需求量,节约能耗。但当发酵液粘度较高时,发酵罐内流体的宏观混合问题就凸现出来,就有可能产生混合分区,气泡尽管得到了局部的分散,但在整个搅拌槽内得不到均匀的分布。所以,宏观混合的问题在中高粘度发酵中与气体的分散同样重要。
右图中彩色箭头表示的是物料的流动方向。可以看出,现发酵罐内采用的是四层径流桨,流体从搅拌器沿径向发散,再从搅拌器的上下吸入,每个搅拌器均产生一个独立的流型,从而产生四个混合分区,各混合分区之间的物质与能量的交换受到了阻碍,宏观混合比较差。
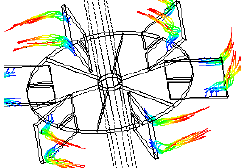
120m3 土霉素发酵罐改造方案
1、合理分配各搅拌器的能耗
改造后本发酵罐的搅拌功率约为165kW,其中55%分配给底层的气体分散涡轮DT604,主要用于气体的分散;其余45%分配给上三层轴流搅拌器SP403,主要用于维持气泡的分散状态和釜内的宏观混合及传热,形成均一的温度场和浓度场,并有利于体系气含率的提高。
六凹叶圆盘涡轮搅拌器
2、桨型选择与流型改善
鉴于原发酵罐搅拌器存在的桨型和流型问题,我们认为可进行以下几方面的改造:
上三层径流桨改为SP403高效轴流桨,使整个搅拌槽内成为一个混合区域,从而消除混合分区。此外,发酵罐内每分钟的循环次数约为5次,增强了气泡的再循环能力,并可提高气含率和氧气的利用率。SP403为宽叶轴流桨,可以兼顾到气液分散和宏观混合两个方面,这对于发酵工艺来说是至关重要的。SP403桨与传统的六直叶圆盘涡轮相比,可提高传质30%;剪切率可降低75%,适用于对剪切敏感的发酵工艺;能耗可降低45%;能够提高对剪切敏感的发酵工艺的得率;
底层六箭叶圆盘涡轮改为DT604六凹叶圆盘涡轮,可防止通气后功率的下降,从而提高气体的分散能力和大气量的处理能力,并可减小对气量的要求。DT604六凹叶圆盘涡轮径向流桨,其叶片型式为最优化设计的非对称抛物面,与传统的六半管叶片圆盘涡轮相比,不仅可以节能30%以上,而且还可以分散更多的气体,并且不会产生大的压降,通气率对搅拌功率的下降影响较小。
搅拌器选择:
120m3土霉素发酵罐搅拌器选型对比
|
|
搅拌机内部情况 | 宏观流场和温度分布均匀性比较 |
1、气体分散叶轮不同
索孚采用的气体分散叶轮为六凹叶圆盘涡轮搅拌器,即DT604搅拌器,叶轮直径为1250mm,叶片高度为250mm,凹面形状为更符合气穴行为的类抛物线曲面,采用专用模具压制,通气后功率变化很小,即功率对气量变化不敏感,特别适合大气量的分散。
DT604搅拌器气含率高,氧利用率也高一些,估计还可能节约10%以上的通气量,这是十分可观的。
其它方案采用的气体分散叶轮为六叶圆弧圆盘涡轮搅拌器,叶轮直径为1250mm,叶片高度为120mm,凹面形状为圆弧面,采用直径为219mm的钢管制造,通气后功率变化相对较大,大气量时搅拌器背面容易产生气穴,导致“打滑”,气体处理能力下降;
2、功率分配不同
|
|
六凹叶圆盘涡轮搅拌器 | CFD流场模拟图 |
由于发酵罐的气体进口位于发酵罐的底部,底部搅拌器(即第1个搅拌器)的分散能力显得十分重要,搅拌的能量消耗应主要集中在此搅拌器,其他位置搅拌器的主要功能是维持气泡的分散状态和釜内的宏观混合及传热,能耗相对较小。
杭州索孚方案中的气体分散叶轮功率占总能耗的55%左右,达90kW。
DT604的设计根据实验结果还可以进一步改进,如采用倾斜的DT604,具有一定的轴流能力,增加底部物料混合效果,也可适当再减小功率。此外,气体分布管的位置也很重要,一般位于2/3桨叶直径处。
其它方案中的气体分散叶轮功率占总能耗的45%左右,仅为73kW,气体分散能力明显较低,搅拌器的能耗分配方案不合理。
3、发酵罐内的流型不尽相同